Clean by Design
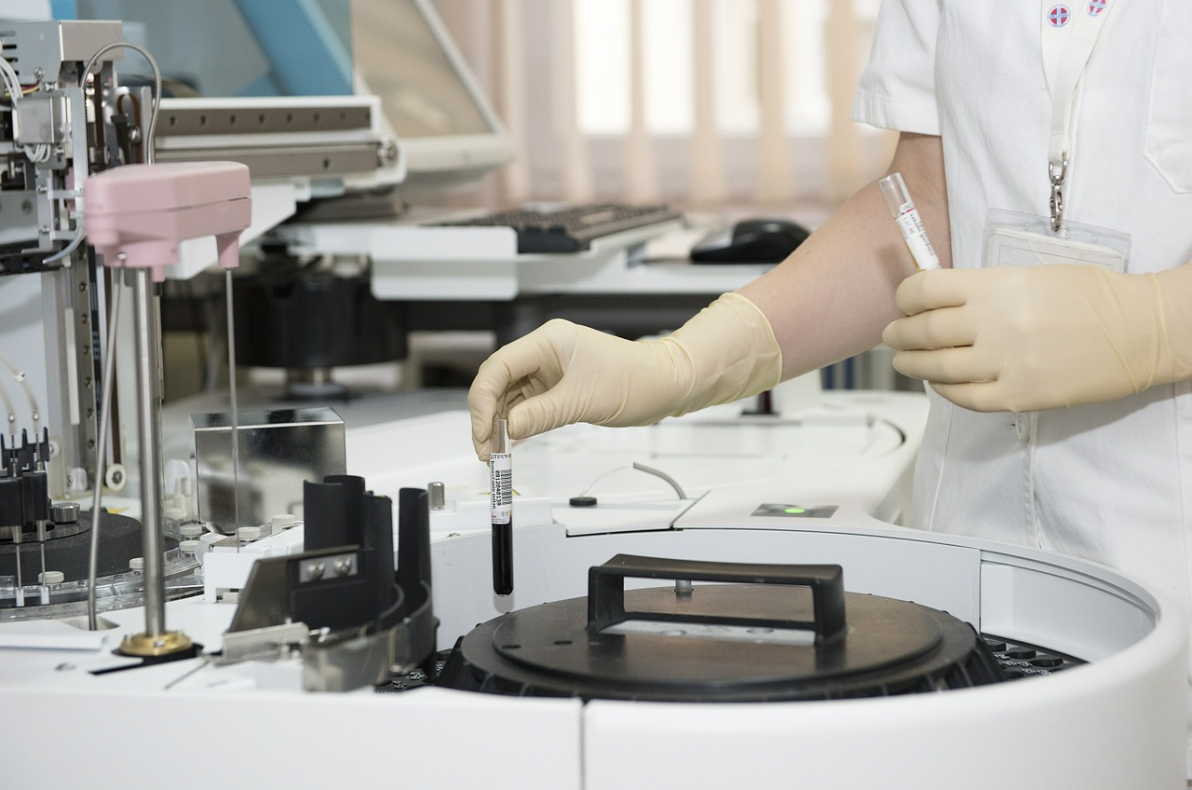
Cleanrooms, often referred to as controlled environments, must be thoughtfully designed and impeccably maintained to keep contaminants out and potentially hazardous materials in. These rooms have garment protocols, specialty disinfectants, and operational requirements, and there are a number of factors that must be considered in maintaining the cleanliness of these rooms. The equipment, disinfectants, and cleaning team entering the controlled environment must meet the required ISO rating, proper gowning materials, cleaning techniques, personal hygiene, and other standards. Crews need to engage in slow and careful movements, as electrostatic discharge can even cause contamination. Surfaces must be wiped in a particular way, and even cleanroom cleaning equipment has its own cleaning protocol. Along the way, measurement and instrumentation will be helpful in mitigating contamination risk, along with developing protocol for major decontamination after maintenance work. Disinfectants must be carefully manufactured, packaged and transported so as not to transmit unwanted matter, and in instances of heavy debris, a detergent must be used first.