My Most Challenging Project
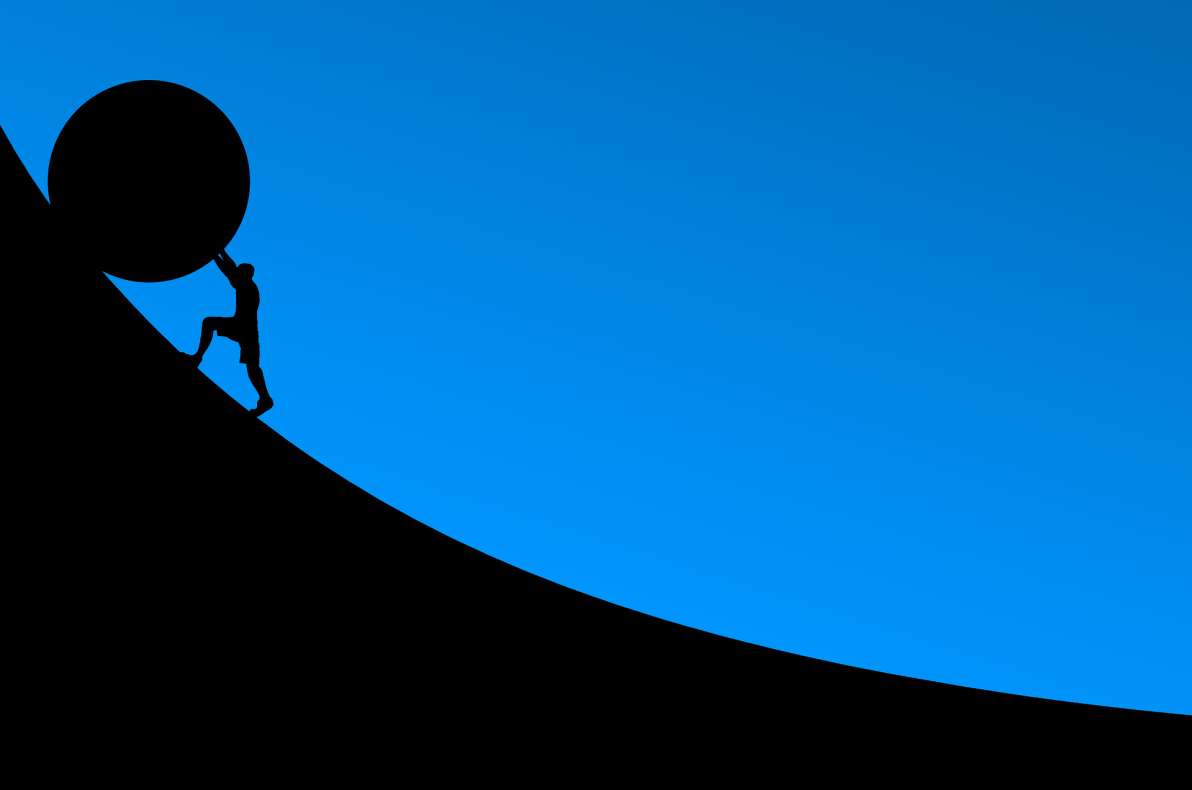
In 2017, C&R launched My Most Challenging Project, a department in which we ask members to share their most difficult projects and lend advice on how others can solve similar challenges. Brian Schraidt of Ideal Restoration recounts a Category 1 water loss at the outpatient wing of a university hospital. The team had to meet a 72-hour drying deadline. Read on to see how Brian and his team managed to get everything done.
What was the project?
The project was a Category 1 water loss in a university hospital outpatient wing. A 2-inch braided stainless steel hot water supply line ruptured in the ceiling above a teaching lab on the second floor. The local shut-off valve was located near where the line ruptured and could not be accessed due to the water temperature, which was over 200 degrees Fahrenheit. Because of this, the water could not be immediately shut off, and a large amount of water was released.
Approximately 40,000 square feet on the first and second floors were affected. The first floor consisted of the loading dock, shipping, receiving, maintenance shop, hazardous materials storage and other support services. Affected areas on the second floor included over 40 offices and administrative rooms, the blood bank, multiple clinical and research labs, and three teaching areas.
Ideal was contacted by the hospital’s facilities management staff at 11:24 p.m. on Sunday night. Ideal’s crews worked with the building engineering staff to extract standing water. Dehumidifiers were set up to reduce the humidity levels in the affected areas. The second floor was prioritized due to the critical nature of the affected areas.
Ideal was initially given a deadline of 72 hours from the time the loss occurred to have all affected materials returned to the dry standard by the hospital’s infection control team. Any materials not returned to the dry standard by the deadline would need to be removed. The deadline to return any affected materials to the dry standard was set for 11 p.m. on Wednesday night.
The hospital staff began packing out the contents, and movers were called in to remove the furniture. Inspection holes were drilled in affected walls to determine the exact makeup of the wall systems. Almost all affected walls were found to have saturated insulation. Working within the laboratories and blood bank while they were in operation was not an option. Closing those areas would require the hospital to shut down the operating rooms. This would significantly impact hospital operations and possibly close the hospital.
Ideal met with key stakeholders and agreed on the following drying plan:
- Ideal would set up drying equipment to dry out affected materials and control humidity.
- The client would contract movers to remove contents from the affected areas, focusing on the walls adjacent to the laboratories and blood bank first.
- Once affected areas were clear of contents, Ideal would erect hard containment and establish negative air pressure. All areas where demolition was to be performed would require containment and engineering controls.
- Once containment was in place, affected walls adjacent to the laboratories and blood bank would be opened and affected insulation would be removed.
- Drying equipment would be set up to dry the affected walls within the laboratories and blood bank from the administrative side
- At 11 p.m. on Wednesday, final moisture readings would be taken to determine what materials would need to be removed.
What were the unique challenge(s) that had to be overcome?
In addition to the typical challenges faced on large water loss projects, this project had its own set of unique challenges that had to be overcome. The biggest challenge was completing the work in compliance with the hospital’s infection prevention and control policy.
An Infection Control Risk Assessment (ICRA) for the project was prepared by the hospital’s infection control and prevention practitioners. This assessment outlines the work practices, technician training requirements and equipment certification requirements. Per the ICRA, all demolition must be done within a hard containment under negative air pressure and have an anteroom for ingress and egress. All negative air machines, air scrubbers and HEPA vacuums were required to be certified by a third party prior to use. All workers must complete the hospital’s ICRA training course provided by the facilities department. All debris removed from the work areas was required to be transported in a covered debris cart. These carts were required to be wiped down in the anteroom prior to leaving the containment area.
Meeting the 72-hour deadline proved to be very difficult. Ideal had to wait for the movers to clear affected areas before containment could be set up. The first area to be cleared of contents and ready for demolition was ready at 3 p.m. Wednesday afternoon, giving Ideal only hours to open up the walls and dry them out.
In addition to the challenges set forth by the ICRA requirements, the time-sensitive nature of the work added its own complexities. The hospital wanted the repair work completed as soon as the demolition was completed and it was verified that all affected materials had been removed. The hospital already had a general contractor working in the building. Ideal worked directly with this contractor to ensure a seamless transition between demolition and repair work.
Working in an active hospital also presented its own challenges with access and logistics. Along with the repair contractor, Ideal had to work side by side with the movers and hospital staff. Although the loss occurred in an outpatient wing, hospital staff were still using the corridor to access the laboratories and blood bank. We were limited to the use of only two elevators, one of which went to the helipad and would be recalled every time a life flight came in. Access was also tightly controlled, such that anyone entering the building, using the elevator or moving between areas was required to have a badge or be escorted by a staff member.
To top it all off, The Joint Commission was on-site first thing Monday morning for their inspection of the entire facility. This made it imperative that all work be completed exactly as specified in the ICRA.
How where those challenges addressed to successfully complete the project?
To meet the ICRA requirements, Ideal held pre-shift meetings with all crews to go over the requirements and expectations. The project manager and two supervisors were also continuously walking the project to ensure all requirements were being followed and ensure a high level of quality control. Workers were rotated out in groups to attend the hospital’s ICRA training. Every effort was made to make sure the work was as low impact on the day-to-day operations as possible. In the corridor adjacent to the work area, walk-off mats were placed on both sides of the entry and exit doors at both ends. A technician was assigned to continuously mop the hallway to remove any dust or debris, and boxes of booties were placed at each entrance to be worn by anyone entering the area.
Ideal’s abatement team was brought in to erect the hard containment. Previous knowledge and experience with building containments proved invaluable in the efficient and rapid erection of the hard containment throughout the project. Delivery of materials for the hard containment was coordinated with Ideal’s warehouse staff. The project manager and warehouse team were in constant communication to ensure the crews on-site had the equipment and materials needed at all times.
A third-party consultant was brought in Monday afternoon to certify all the HEPA equipment. They were stationed at the entrance, and each piece of equipment was tested and certified as it was brought on-site. This ensured that no equipment without a certification sticker ended up in any of the work areas.
When the first area was finally ready for demolition on Wednesday afternoon, crews were already on-site, ready to begin work. Demolition was performed quickly, and drying equipment was immediately set up to optimize drying conditions. A combination of large-capacity dehumidifiers, compact electric heaters and air movers were utilized to accelerate the drying process.
At the 11 p.m. deadline on Wednesday, moisture readings were taken and documented. A meeting with the hospital was scheduled for noon the following day to review the findings.
Ideal kept in constant communication with not only the hospital staff but with the movers, repair contractor and engineering team. This constant communication and coordination made a chaotic and difficult situation much more manageable for all involved. This communication continued long past the first 72 hours and was key in delivering a successful project.
How did the project turn out?
At the 72-hour deadline, only a portion of the affected walls had been returned to the dry standard. A significant amount of wall material would need to be removed in the coming weeks. All removal would be completed according to the ICRA protocol. However, because of the diligence and strict adherence to the ICRA protocol by Ideal during the emergency response, the hospital stakeholders modified the removal requirements. All wall material that was documented as affected in the initial moisture survey would need to be removed. The exception to this would be the interior walls of the laborites and blood bank. As long as those walls were dry when the back side was opened up and there were no signs of microbial growth, they could remain in place. This prevented the need to partially or completely close any of those areas. The project was completed to the client’s satisfaction, and the hospital is a repeat client.
Much to the relief of all involved, the hospital also passed the inspection by The Joint Commission.
What lessons were learned from the project that can be shared with fellow RIA members that can be applied on the next challenging project?
The main lesson learned from this project was that every client has different needs and priorities. In order to successfully complete challenging and complex projects, define those needs, establish their priorities early and exceed their expectations. This will build a long-lasting relationship based on trust and understanding. Getting to know your client’s expectations and priorities before they ever need to call you will take you even further. Knowing exactly what your client expects from you out of the gate goes a long way to completing a successful project.
At the end of the day, the client knew that asking for everything to be dry within 72 hours was a daunting task. However, due to our stringent adherence to their ICRA protocol, we were kept on to complete the rest of the work. This attention to detail and the client’s priorities are what made this extremely challenging project a success, for Ideal and customer alike.
Second, if you are going to take on specialty work such as hospitals or other health care, do your research and get educated. Clients will look to you as the subject matter expert. Take the time to research and understand what will be expected of you on these types of projects.
Finally, and this should go without saying, but communication is critical in situations like this. With so many moving parts, even small miscommunications can be lead to big issues. Take the time to learn the key players on every project and go out of your way to communicate and work with them. Internal communication must be as streamlined as the external communication. Without seamless communication among the field, office and warehouse teams, this project would not have run nearly as smoothly and efficiently.
Brian Schraidt joined the Ideal team as a summer intern in 2012 after meeting CEO Jaclyn Carpenter during a work-study program at the annual RIA convention. After graduating from Purdue University with a degree in construction management, specializing in disaster restoration, Brian returned to Ideal where he worked in the field to gain hands-on experience on a wide variety of restoration projects. He was promoted to his current position as the project manager in January 2015. Today, Brian’s main focus is providing comprehensive solutions for water damage projects, specializing in health care and hospitals.