My Most Challenging Project
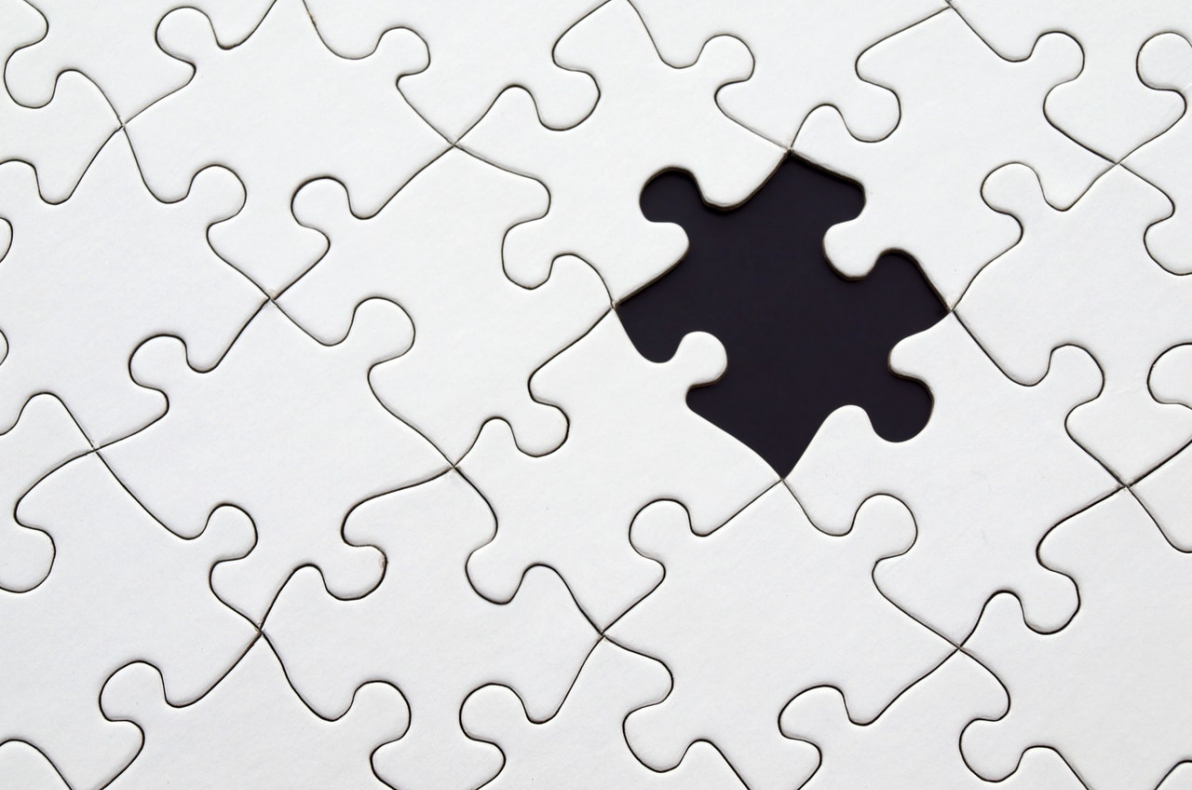
In 2017, C&R launched a department titled “My Most Challenging Project,” in which we ask members to share their most difficult projects and lend advice on how others can solve similar challenges. Joe Meyers, CR, WLS, CMP, RTPE 0005, project manager and branch manager for Hammer Restoration was contacted by a third-party administrator (TPA) to perform mitigation services on a 10,000-square-foot, two-story religious retreat center. After the project commenced, chaos ensued. Read on the see how Meyers navigated the chaos and came out on top.
What Were the Challenges?
Hammer Restoration, established in 1964, is a family-owned business serving all of Michigan from its two locations in Saginaw and Mount Pleasant.
Hammer was contacted by a third-party administrator (TPA) to perform mitigation services on a 10,000-square-foot, two-story religious retreat center in a very rural area approximately two hours from our location. The retreat had 12 suites, each with its own bath and outside access, as well as a large kitchen and gathering area. The structure was typical wood frame construction with a brick and vinyl exterior.
The project started out very challenging due to the TPA declaring an extremely low insurance limit. The structure’s significant electrical distribution system showed evidence of water damage and was determined to be unable to safely provide the needed power, so a power diesel generator was secured. Due to the rural location of the site, we were unable to arrange for delivery of diesel fuel to the site and had to refuel the generator by using a pickup truck and fuel pod. This required many trips each day. The TPA also wanted total control over the mitigation and remediation process. Several building envelope issues were discovered, along with mold growth. The exterior brick was installed almost in direct contact with the vapor retarder membrane with no apparent drainage plane. Compounding the problem, at some point, concrete aprons were poured and not only sloped toward the building but also covered most of the weep holes in the brick face. This allowed rainwater to pool and a direct path into the framing via capillary action and vapor diffusion through the brick face. The TPA wanted all work stopped until they could hire a hygienist of their choosing to evaluate the growth, set remediation protocol and put the project out to bid. During all this, a second supply line failed and re-wet approximately 60 percent of the structure overnight while we were in a stabilization phase.
How Did You Overcome These Challenges?
We made a conscious decision to temporarily cease communication with the TPA. Some of the factors that went into the decision were the size of the loss, the very rural location and, in our opinion, the unreasonable request made by the TPA. We kept the structure in the pre-restoration stabilization phase being confident we were qualified to perform the mitigation and, with the help of a local Indoor Environmental Professional (IEP), developed a remediation strategy. Controlled removal of non-salvageable wet materials proceeded in accordance with the IEP’s protocol. Once removal/remediation was completed and clearance testing validated the work, the structure was then placed into a carefully designed and monitored restorative drying phase. The insurance carrier’s representative met us on-site and, after an extensive walk-through and scope discussion, agreed with our assessment and strategies.
What Lessons Did You Learn That Could Be Applied to Future Projects?
It is important that professional restorers possess the education, experience and understanding of construction techniques in their area to recognize the possible negative effects and how improperly installed components can potentially affect the building and its occupants. It is often beneficial to consult specialized experts to help determine the scope of work. While I feel that I have fairly comprehensive knowledge of building technologies, I believe the knowledge gained while on the path for advanced designations the RIA offers, such as Certified Restorer, was invaluable in recognizing the issues with the brick face, concrete apron and apparent lack of drainage plane.
Early in the project, we retained the services of Ken Larsen, CR, WLS, CMP, CSDD, owner of International Dry Standard Organization, to assure our stabilization and restorative drying strategies were sound and validated for the TPA. We were ultimately successful in the end: We came to a resolution with the TPA on the mitigation/remediation, and still to this day maintain an amicable relationship. We were able to complete the reconstruction portion of this loss while working with the property owners and the insurance carrier. We, as restorers, should always speak for the needs of the structure with impartial professionalism. Every restorer should actively seek knowledge and strive to obtain the advanced designations available.