Wall & Cavity Drying: Reaching Full Drying Potential
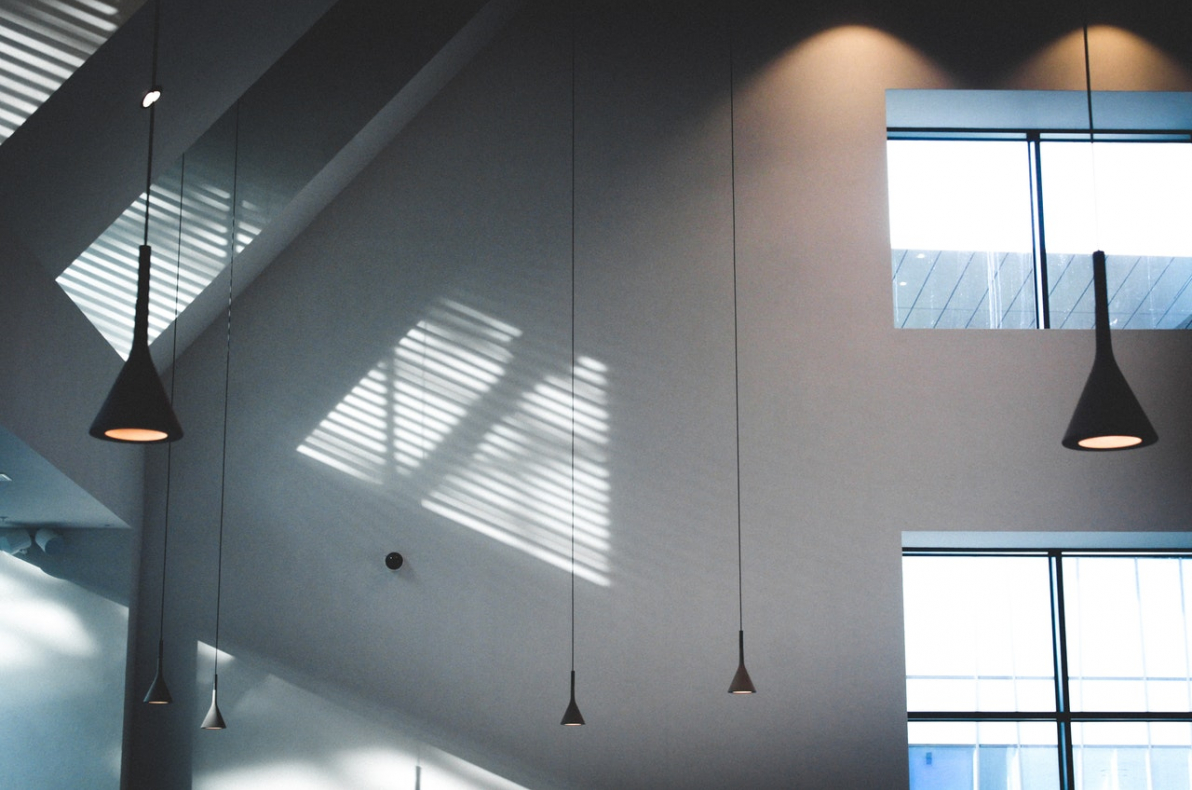
Building materials are more and more advanced and focused on energy efficiency. Materials range from insulated concrete bases and insulated block walls to a wide variety of insulation materials and vapor barriers. Drying wall cavities, crawlspaces, and other interstitial spaces continues to be a struggle, but injection drying systems can quickly and efficiently deliver dry air directly to the water and increase the success rates of drying, which can reduce the amount of strip-out work required and lessen the risk of secondary damage. These systems result in better levels of service for the client, a reduction in drying times, and a healthier result for everyone involved. Now, some injection drying solutions can be attached directly to the heat source, making the drying process more evenly distributed into cavities and tight spaces without the need to heat the entire living space. These types of injectors are less intrusive and still provide a significant amount of warm, dry air with holes that are small enough to maintain fire-rated wall integrity. They also offer a base unit that adds a limited amount of noise to your environment. Another option is target drying that can be connected directly to a precision auxiliary heater, and air movement is typically provided by the air movers you already have on the job. Wall-specific drying mats are designed to inflate and hold themselves against the wall, and micro-jets along the entire surface of both wall and floor ensure even heating all the way to the sill plate. No one tool can do every job. The size and severity of the loss, indoor and outdoor environments, and even the access you have to the space you need to dry all affect which equipment you decide to employ on a job.